高频感应加热设备根据设备所输出的交变电流的频率高低不同,可分为:中频感应加热,超音频感应加热(高频感应加热)超高频感应加热。由于交变电流在导体中流动时存在着集肤效应,即,随着感应电流的频率升高,电流会趋向于导体的表层流过。
高频感应加热设备加热方式的比较:
中频感应加热方式
频率范围:一般1KHZ至20KHZ左右,典型值是8-12KHZ左右。加热深度、厚度约3-10mm。多用于较大工件,大直径轴类,大直径厚壁管材,大模数齿轮等工件的加热、退火、回火、调质和表面淬火及较小直径的棒材红冲、煅压等。
超音频感应加热(高频感应加热)方式
频率范围:一般30KHZ-80KHZ左右)。加热深度、厚度,约2-3mm。多用于中等直径的工件深层加热、退火、回火、调质,较大直径的薄壁管材加热、焊接、热装配,中等齿轮淬火等。小型工件的深层加热、红冲、煅压、退火、回火、调质,表面淬火,中等直径的管材加热和焊接、热装配,小齿轮淬火等。
超高频感应加热方式
频率相对*高,频率范围:一般200KHZ以上,可高达几十MHZ。加热深度、厚度*小,约0.1-1mm。多用于局部的极小部位或极细的棒材淬火、焊接,小型工件的表面淬火等。
感应式加热的主要优点和缺点:
1)对工件无需整体加热,可有选择性地进行局部加热,因而电能消耗少,工件变形小。
2)加热速度快,可使工件在极短的时间内达到所需温度,甚至1秒以内。从而使工件的表面氧化和脱碳都较轻,大多数工件都无须气体保护。
3)可根据需要通过调整设备的工作频率和功率,对表面淬硬层进行调控。从而使淬硬层的马氏体组织较细,硬度、强度和韧性都比较高。
4)经感应加热方式热处理后的工件,表面硬层下有较厚的韧性区域,具有较好的压缩内应力,使工件的抗疲劳和破断能力都更高。
5)加热设备便于安装在生产线上,易于实现机械化和自动化,便于管理,可有效地减少运输,节约人力,提高生产效率。
6)一机多用。即可完成淬火、退火、回火、正火、调质等热处理工艺,又可完成焊接、熔炼、热装配、热拆卸及透热成形等工作。
7)使用方便、操作简单、可随时开启或停止。且无须预热。
8)即可手动操作,也可半自动和全自动操作;即可长时间地连继工作,亦可即用即停随机使用。有利于设备在供电低谷电价优惠期的使用。
9)电能利用率高,环保节能,**可靠,工人工作条件好,国家提倡。等等.
感应加热设备的选择 ,高频感应加热设备的应用
如何选择、选用感应加热设备呢?主要要从几个方面考虑:
被加热的工件形状和尺寸
工件大、棒料、实材,应选用相对功率大,频率低的感应加热设备;工件小、管材、板材、齿轮等,则选用相对功率小,频率高的感应加热设备。
需要加热的深度和面积
加热深度深,面积大,整体加热,应选用功率大,频率低的感应加热设备;加热深度浅,面积小,局部加热,选用相对功率小,频率高的感应加热设备。
所需的加热速度
需要的加热速度快,应选用功率相对较大,频率相对较高的感应加热设备。
4)设备的连继工作时间
连续工作时间长,相对选用功率略大的感应加热设备。
5)感应部件与设备的连线距离
连线长,甚至需要使用水冷电缆连接,应相对选用功率较大的感应加热设备。
6)工艺要求
一般来说,淬火、焊接等工艺,相对可以功率选小一些,频率选高一些;退火、回火等工艺,相对功率选大一些,频率选低一些;红冲、热煅、熔炼等,需要透热效果好的工艺,则功率应选得更大,频率选得更低。
7)工件的材料
金属材料中熔点高的相对选用功率大一些,熔点低的相对选用功率小一些;电阻率小的选用功率大一些,电阻率大的选用功率小一些。等等。
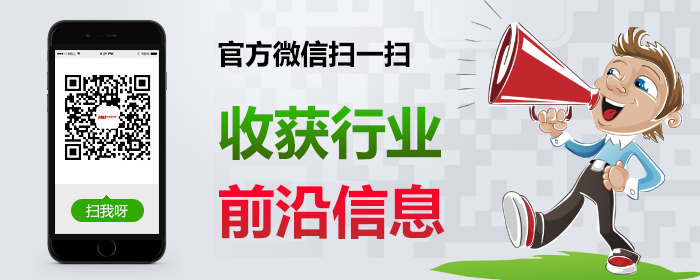