其实一直在强调染色方面色差仪的应用特别广泛,之前一直没有细说,现在我们就来说说色差仪在涤棉长车染**差方面的控制,色差仪的原理我就不再说了大家一定也清楚了,色差仪的应用可以操作正确、快速的分析出色差的产生原因。首先介绍一下色差:
色差可分为以下四类:
原样色差:指染色纺织物在色相、色泽深度上与客户提供的样品或标准色卡样的差异;
前后色差:不同时间然出的同一色号纺织物在色相和色泽深度上的差异;
左中右色差:在纺织物品上,左、中、右不同部位色相和色泽深度的差异;
正反色差:织物正面与反面的色相与色泽深度不一致。
通过分析我们可以从不同的角度利用色差仪和电脑的色彩管理数据库来控制涤棉长车染色过程中的色差。
原样色差的预防与控制
从原样色差的定义不难看出,这种色差是非常明显的一眼就能发现,色差仪测量出来数值偏差比较大的,原样色差主要是由拼色的染料选择不合理和机台染色时**调整 不当造成的。为了防止这种现象的出现我们采用减少染料的种类可以减少染料之间的相互干扰;**中尽量用较接近原样色相的染染拼混;尽量应用具有相似上染性能的染料。同时在选择染料时尽量用色差仪对样品和原样多做测量,记录色彩数据,色差仪的测量结果比我们目测的准确很多,又不会受到客观因素影响,所以在色差避免这块我们的色差仪的应用就不容放松。
色差仪的测量、分析、确定染料,然后织物染色,在之后一般要进行柔软、防水、抗静电、轧光等工序,这些整理剂总会对色光有影响在调整色光时应考虑到这些因素。
前后色差的预防与控制
前后色差其实就是批次间的色差,这主要是由化料、机械设备的性能、半制品的质量、工艺参数及条件的变化这四个方面引起。染同一色泽的织物,要用相同的前处理工艺。这样在色差仪的检测过程中色差值才会很小。染色工艺中染浅色是选择白度较一致的染坯,*好也是色差仪测量白度在规定的范围内,两批次的白度值相差较少。准确称料、化料。称料前要校对秤是否准确,称料时按照**准确称料,称好料后把染料桶盖好,以纺染料吸收空气中的水份或染料中的水份被空气吸收,这样会影响染料的比重。整个过程也要多次成样,把这些样品用色差仪这行色彩管理在于原样比较,记录色彩数据。
左中右色差的预防和控制
左中右色差的形成是我们*容易理解的,我们几乎所有的物品用色差仪测量,左中右都是以一定的色差值的,只是有的明显有的肉眼几乎看不见。肉眼看不见的色差我们就不谈论了,只有学术上才会关心这块,纺织染色我们只关心肉眼可以看见的,色差仪测量数据偏差较大的。左中右色差是由轧辊压力和织物所受热处理这两个方面引起的,我们为了减小甚至避免这种色差就应该轧车左中右压力要保持一致。织物浸轧染液后,如轧辊压力不一致,会使织物左中右带液量不等而产生左中右深度上的差异。在轧分散染料时如出现左中右色差应及时调整,绝不能套在套有其他染料时调整,这样会出现织物的左中右在色相上产生差异,这是因为涤与棉的色相不可能完全一致。
正反色差的预防与控制
如果真的在色差仪的测量结果中发现正反色差,那一定是生产织物的正反两面受热不一致造成的。这种受热不一致在浸轧染液烘干过程中和热熔固色两方面都有可能产生。前这是由于染料产生泳移所致;后这是由于染料热熔固作条件产生变化所致。
其它影响
坯布选用不当:由于坯布采用的纤维种类、质量、配棉的变化,以及上浆情况对染色均有较大影响,所以,不同厂家的坯布在相同的染色工艺下,加工所得色泽往往深浅不一。这就要求我们在采购坯布时,及时了解纺织厂的织造工艺情况,并做到同一个颜色用同一厂家的坯布,以防因坯布问题造成色差。这就要求我们这整个选料、染色、成品过程中高频度的应用色差仪和电脑计录色彩数据,形成色彩数据库,在比较和沟通中选择*适合当次染色的所有工序。
综上所述,利用色差仪控制涤棉长车染**差是一个繁琐而复杂的过程,但也是不可忽视的过程,在染色整个过程注意和色差仪的测量完整较高的话,意味着成品的色差越小,客户的满意程度越高,产品的品质和外观越**。
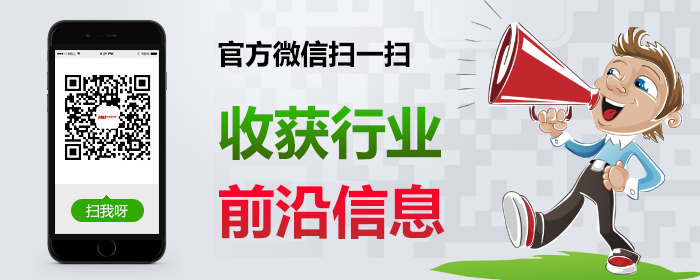