一 . 常用热处理炉炉型的选择
炉型的选择,炉型应依据不同的工艺要求及工件的类型来决定:
1 .对于不能成批定型生产的,工件大小不相等的,种类较多的,要求工艺上具有通用性、 多用性的,可选用箱式炉。
2 .加热长轴类及长的丝杆,管子等工件时,可选用深井式电炉。
3 .小批量的渗碳零件,可选用井式气体渗碳炉。
4 .对于大批量的汽车、拖拉机齿轮等零件的生产可选连续式渗碳生产线或箱式多用炉。
5 .对冲压件板材坯料的加热大批量生产时,*好选用滚动炉,辊底炉。
6 .对成批的定型零件,生产上可选用推杆式或传送带式电阻炉(推杆炉或铸带炉)。
7 .小型机械零件如:螺钉,螺母等可选用振底式炉或网带式炉。
8 .钢球及滚柱热处理可选用内螺旋的回转管炉。
9 .有色金属锭坯在大批量生产时可用推杆式炉,而对有色金属小零件及材料可用空气循环加热炉。
二 . 加热缺陷及控制
一 ) 、过热现象
我们知道热处理过程中加热过热*易导致奥氏体晶粒的粗大,使零件的机械性能下降。
1. 一般过热:加热温度过高或在高温下保温时间过长,引起奥氏体晶粒粗化称为过热。粗大的奥氏体晶粒会导致钢的强韧性降低,脆性转变温度升高,增加淬火时的变形开裂倾向。而导致过热的原因是炉温仪表失控或混料(常为不懂工艺发生的)。过热组织可经退火、正火或多次高温回火后,在正常情况下重新奥氏化使晶粒细化。
2. 断口遗传:有过热组织的钢材,重新加热淬火后,虽能使奥氏体晶粒细化,但有时仍出现粗大颗粒状断口。产生断口遗传的理论争议较多,一般认为曾因加热温度过高而使MnS 之类的杂物溶入奥氏体并富集于晶界面,而冷却时这些夹杂物又会沿晶界面析出,受冲击时易沿粗大奧氏体晶界断裂。
3.粗大组织的遗传:有粗大马氏体、贝氏体、魏氏体组织的钢件重新奥氏化时,以慢速加热到常规的淬火温度,甚至再低一些,其奥氏体晶粒仍然是粗大的,这种现象称为组织遗传性。要消除粗大组织的遗传性,可采用中间退火或多次高温回火处理。
二 ) 、过烧现象
加热温度过高,不仅引起奥氏体晶粒粗大,而且晶界局部出现氧化或熔化,导致晶界弱化,称为过烧。钢过烧后性能严重恶化,淬火时形成龟裂。过烧组织无法恢复,只能报废。因此在工作中要避免过烧的发生。
三 ) 、脱碳和氧化
钢在加热时,表层的碳与介质(或气氛)中的氧、氢、二氧化碳及水蒸气等发生反应,降低了表层碳浓度称为脱碳,脱碳钢淬火后表面硬度、疲劳强度及耐磨性降低,而且表面形成残余拉应力易形成表面网状裂纹。加热时,钢表层的铁及合金与元素与介质(或气氛)中的氧、二氧化碳、水蒸气等发生反应生成氧化物膜的现象称为氧化。高温(一般 570度以上)工件氧化后尺寸精度和表面光亮度恶化,具有氧化膜的淬透性差的钢件易出现淬火软点。为了防止氧化和减少脱碳的措施有:工件表面涂料,用不锈钢箔包装密封加热、采用盐浴炉加热、采用保护气氛加热(如净化后的惰性气体、控制炉内碳势)、火焰燃烧炉(使炉气呈还原性)。
四 ) 、氢脆现象
高强度钢在富氢气氛中加热时出现塑性和韧性降低的现象称为氢脆。出现氢脆的工件通过除氢处理(如回火、时效等)也能消除氢脆,采用真空、低氢气氛或惰性气氛加热可避免氢脆。象现在的连续热处理炉淬火后及时回火处理时可在回火过程中兼顾驱氧处理,跟据目前的使用和统计情况看在连续式可控气氛热处理炉所处理的产品一般是不会出现氢脆现象的。
当然,任何事都有它的两面性,实际工作中有人利用此现象来为人服务(如合金的粉碎处理等)。
三.热处理应力及其影响
热处理残余力是指工件经热处理后*终残存下来的应力 , 对工件的形状 , 尺寸和性能都有极为重要的影响。当它超过材料的屈服强度时 ,便引起工件的变形 , 超过材料的强度极限时就会使工件开裂 , 这是它有害的一面 , 应当减少和消除。但在一定条件下控制应力使之合理分布, 就可以提高零件的机械性能和使用寿命 , 变有害为有利。分析钢在热处理过程中应力的分布和变化规律 ,使之合理分布对提高产品质量有着深远的实际意义。例如关于表层残余压应力的合理分布对零件使用寿命的影响问题已经引起了人们的广泛重视。
一 ) 、钢的热处理应力
工件在加热和冷却过程中 , 由于表层和心部的冷却速度和时间的不一致 , 形成温差,就会导致体积膨胀和收缩不均而产生应力 ,即热应力。在热应力的作用下 , 由于表层开始温度低于心部 , 收缩也大于心部而使心部受拉 ,当冷却结束时,由于心部*后冷却体积收缩不能自由进行而使表层受压心部受拉。即在热应力的作用下*终使工件表层受压而心部受拉。这种现象受到冷却速度, 材料成分和热处理工艺等因素的影响。当冷却速度愈快 , 含碳量和合金成分愈高 , 冷却过程中在热应力作用下产生的不均匀塑性变形愈大, *后形成的残余应力就愈大。另一方面钢在热处理过程中由于组织的变化即奥氏体向马氏体转变时 , 因比容的增大会伴随工件体积的膨胀 ,工件各部位先后相变,造成体积长大不一致而产生组织应力。组织应力变化的*终结果是表层受拉应力 , 心部受压应力 ,恰好与热应力相反。组织应力的大小与工件在马氏体相变区的冷却速度 , 形状,材料的化学成分等因素有关。
实践证明 , 任何工件在热处理过程中 , 只要有相变 ,热应力和组织应力都会发生。只不过热应力在组织转变以前就已经产生了,而组织应力则是在组织转变过程中产生的 , 在整个冷却过程中 ,热应力与组织应力综合作用的结果 , 就是工件中实际存在的应力。这两种应力综合作用的结果是十分复杂的 , 受着许多因素的影响 ,如成分、形状、热处理工艺等。就其发展过程来说只有两种类型 , 即热应力和组织应力 , 作用方向相反时二者抵消 ,作用方向相同时二者相互迭加。不管是相互抵消还是相互迭加 , 两个应力应有一个占主导因素 , 热应力占主导地位时的作用结果是工件心部受拉, 表面受压。组织应力占主导地位时的作用结果是工件心部受压表面受拉。
二 ) 、热处理应力对淬火裂纹的影响
存在于淬火件不同部位上能引起应力集中的因素 ( 包括冶金缺陷在内 ), 对淬火裂纹的产生都有促进作用 , 但只有在拉应力场内 (尤其是在*大拉应力下 ) 才会表现出来 , 若在压应力场内并无促裂作用。
淬火冷却速度是一个能影响淬火质量并决定残余应力的重要因素 ,也是一个能对淬火裂纹赋于重要乃至决定性影响的因素。为了达到淬火的目的,通常必须加速零件在高温段内的冷却速度 ,并使之超过钢的临界淬火冷却速度才能得到马氏体组织。就残余应力而论 , 这样做由于能增加抵消组织应力作用的热应力值 ,故能减少工件表面上的拉应力而达到抑制纵裂的目的。其效果将随高温冷却速度的加快而增大。而且 , 在能淬透的情况下 , 截面尺寸越大的工件, 虽然实际冷却速度更缓 , 开裂的危险性却反而愈大。这一切都是由于这类钢的热应力随尺寸的增大实际冷却速度减慢 , 热应力减小 ,组织应力随尺寸的增大而增加 ,*后形成以组织应力为主的拉应力作用在工件表面的作用特点造成的。并与冷却愈慢应力愈小的传统观念大相径庭。对这类钢件而言 ,在正常条件下淬火的高淬透性钢件中只能形成纵裂。避免淬裂的可靠原则是设法尽量减小截面内外马氏体转变的不等时性。仅仅实行马氏体转变区内的缓冷却不足以预防纵裂的形成。一般情况下只能产生在非淬透性件中的弧裂, 虽以整体快速冷却为必要的形成条件,可是它的真正形成原因 , 却不在快速冷却 ( 包括马氏体转变区内 ) 本身 ,而是淬火件局部位置 ( 由几何结构决定 ), 在高温临界温度区内的冷却速度显著减缓 ,因而没有淬硬所致。产生在大型非淬透性件中的横断和纵劈 , 是由以热应力为主要成份的残余拉应力作用在淬火件中心 ,而在淬火件末淬硬的截面中心处 , 首先形成裂纹并由内往外扩展而造成的。为了避免这类裂纹产生,往往使用水 --油双液淬火工艺。在此工艺中实施高温段内的快速冷却 , 目的仅仅在于确保外层金属得到马氏体组织 , 而从内应力的角度来看 ,这时快冷有害无益。其次 , 冷却后期缓冷的目的 , 主要不是为了降低马氏体相变的膨胀速度和组织应力值 ,而在于尽量减小截面温差和截面中心部位金属的收缩速度 , 从而达到减小应力值和*终抑制淬裂的目的。
三 ) 、残余压应力对工件的影响
渗碳表面强化作为提高工件的疲劳强度的方法应用得很广泛的原因。一方面是由于它能有效的增加工件表面的强度和硬度,提高工件的耐磨性,另一方面是渗碳能有效的改善工件的应力分布, 在工件表面层获得较大的残余压应力 , 提高工件的疲劳强度。如果在渗碳后再进行等温淬火将会增加表层残余压应力 ,使疲劳强度得到进一步的提高。
等温淬火比通常的淬火低温回火工艺具有更高的表面残余压应力。等温淬火后即使进行低温回火 ,其表面残余压应力,也比淬火后低温回火高。因此可以得出这样一个结论 , 即渗碳后等温淬火比通常的渗碳淬火低温回火获得的表面残余压应力更高,从表面层残余压应力对疲劳抗力的有利影响的观点来看,渗碳等温淬火工艺是提高渗碳件疲劳强度的有效方法。渗碳淬火工艺为什么能获得表层残余压应力? 渗碳等温淬火为什么能获得更大的表层残余压应力 ? 其主要原因有两个:一个原因是表层高碳马氏体比容比心部低碳马氏体的比容大 ,淬火后表层体积膨胀大 , 而心部低碳马氏体体积膨胀小 , 制约了表层的自由膨胀 ,造成表层受压心部受拉的应力状态。而另一个更重要的原因是高碳过冷奥氏体向马氏体转变的开始转变温度( Ms ) ,比心部含碳量低的过冷奥氏体向马氏体转变的开始温度( Ms )低。这就是说在淬火过程中往往是心部首先产生马氏体转变引起心部体积膨胀 ,并获得强化 , 而表面还末冷却到其对应的马氏体开始转变点( Ms ) , 故仍处于过冷奥氏体状态 , 具有良好的塑性 ,不会对心部马氏体转变的体积膨胀起严重的压制作用。随着淬火冷却温度的不断下降使表层温度降到该处的( Ms )点以下 ,表层产生马氏体转变 , 引起表层体积的膨胀。但心部此时早已转变为马氏体而强化 , 所以心部对表层的体积膨胀将会起很大的压制作用 ,使表层获得残余压应力。而在渗碳后进行等温淬火时,当等温温度在渗碳层的马氏体开始转变温度( Ms )以上 , 心部的马氏体开始转变温度(Ms )点以下的适当温度等温淬火 , 比连续冷却淬火更能保证这种转变的先后顺序的特点 (即保证表层马氏体转变仅仅产生于等温后的冷却过程中 ) 。当然渗碳后等温淬火的等温温度和等温时间对表层残余应力的大小有很大的影响。有人对35SiMn2MoV 钢试样渗碳后在 260 ℃和 320 ℃等温 40 分钟后的表面残余应力进行过测试 , 其结果如表 2 。 由表2 可知在 260 ℃行动等温比在 320 ℃等温的表面残余应力要高出一倍多 表 2 。 35SiMn2MoV钢不同等温温度的表面残余应力。
四 . 回火脆性
淬火钢回火时 , 随着 回火温度的升高 , 通常其强度 ,硬度降低,而塑性,韧性提高。但在某些温度范围内回火时,钢的冲击韧性不仅没有提高,反而显著降低,这种脆化现象称为回火脆性。因此,一般不在 250 - 350度进行回火,这就是因为淬火钢在这个温度范围内回火时要发生回火脆性。这种回火脆性称为低温回火脆性或**类回火脆性。**类回火脆性一旦产生就无法消除, 因此生产中一般不在此温度范围内回火。
含有铬、锰、铬 - 镍等元素的合金钢淬火后 , 在脆化温度 (400 ~ 500 ℃ ) 区回火 ,或经更高温度回后缓慢冷却通过脆化温度区所产生的脆性 , 称为**类回火脆性 ,又称高温回火脆性。这种脆性可通过高于脆化温度的再次回火后的快冷来消除。
产生低温回火脆性的原因,目前还不十分清楚。一般认为是由于碳化物以断续的薄片状沿马氏体片或马氏体条的界面析出所造成的。这种硬而脆的薄片碳化物与马氏体间的结合较弱,降低了马氏体晶界处的强度,因而使冲击韧性反而下降。
长沙笃林机电设备有限公司欢迎您来电咨询,洽谈:0731-88672948,0731-88654873
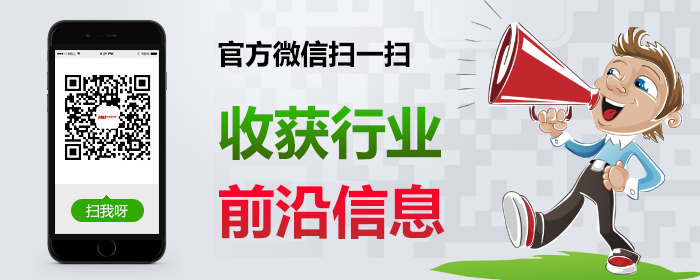