数字电源的实现与进展
数字电源有几种不同的含意,实现方式也各不相同。
*简单的是数字检测,包括监视开关电源的状态,如温度、输入/出电流、输入/出电压、开关频率(占空比)等,并根据需求向主机报告。故障状态信息甚至时间标记等信息可以存储在非易失性存储器中,并在将来某个时间上报这些信息。
**个定义是在“数字检测”的基础上通过数字接口控制开关电源,一般是通过I2C或类似的数字总线控制输出电压、 开关频率、多通道电源的(上/下电)排序、上升斜率、跟踪、(软)启动、裕度控制、故障保护等等。实际上,目前市场上的很多电源管理集成电路都以这种方式工作。
第三个定义是用数字电路彻底取代开关电源中的所有模拟电路,这是真正的原生数字电源。只须编写几行简单的代码,一个核心数字电源集成电路就 可以配置成升压稳压器、降压稳压器、负输出、SEPIC、反激式或正激式转换器,这样将使开关电源更容易设计、配置而且更稳定。但要实现这点从目前看来是相当困难的,因为从物理定律上来说,电流是模拟信号,即使用ADC和DSP取代误差放大器和脉冲宽度调制器的数字开关电源也仍然需要电压基准、电流检测电 路和FET驱动器,这些组件目前只有模拟形式的产品。此外,电感器、变压器以及电容器等模拟元器件在实现数字电源时也是不能没有的。
传统的模拟电源是以模拟控制环路为基础的,如果在模拟控制环路外添加模拟量采样、量化电路,并辅以通信电路,即可构成上面**个定义中所指的带数字检测的比较初级的数字电源。
目前的数字电源大都是按照上面**个定义(即数字控制+数字监视)实现的,电源内部的模拟控制环路由数字控制环路替代。未来是属于数字电源的,但数字化是个渐进的过程,其发展很可能由同时使用模拟和数字技术的混合系统开始,进而演进到全数字实现。以前,数字化是以采用高成本的复杂多芯片电路方案为代价的。例如,一个具有电压、电流监视及控制能力的应用可能需要很多集成电路,如高稳定度基准源、高精度多通道ADC、DAC和专用微控制器,此外还需要不小的软件开发工作量。如果再考虑成本、复杂性、线路板空间限制和严苛的产品上市时间要求,以数字方式管理电源的确需要人们付出不菲的代价。
*近出现的数字电源产品的集成度和易用性已经达到一个更高的高度。包括传统的模拟电源厂商和新兴的数字电源芯片设计厂商在内的大部分厂商都在着手解决纯粹的电源转换以外的问题,包括添加监测功能,提供可与系统通信的数字接口,以及建立数字控制反馈环路,即在模拟变换器外面使用“ 数字外壳”。常见的方案有两种:(1)单芯片控制器方案。通过外接A/D转换芯片进行取样,取样后对得到的数据进行运算处理,再把结果通过D/A转换后传送到PWM芯片,从而实现单芯片控制器对开关电源的控制。这种方案的技术目前已经比较成熟,设计方法容易掌握,而且对单芯片控制器的要求不高,成本比较低。但是整套电路用到多个芯片,电路比较复杂;且经过A/D和D/A转换等步骤,会造成比较大的信号延迟,进而影响电源的动态性能和稳压精度。有些单芯片控制器整合了PWM输出,但一般单芯片控制器的运行频率有限,无法产生足够高的频率和精度的PWM输出信号。(2)通过高性能数字芯片(如 DSP或MCU)对电源实现直接控制的方案。数字芯片完成信号采样、处理和PWM输出等工作。由于数字PWM输出的信号功率不足以驱动开关管,一般还需通过一个驱动芯片驱动开关管,即数字控制器与功率级之间的接口由MOSFET驱动器提供。由于这些数字芯片有较高的取样速度(DSP片内的AD转换器完成一 次A/D转换只需数百纳秒,相较之下,一般8位MCU控制器要数微秒之久)和指令周期,输出的PWM信号的分辨率仅数百皮秒,过流检测和关闭电源仅须数十纳秒,可以快速有效的实现各种复杂的控制算法,使设计具备较高的动态性能和稳压精度。此外,在微处理器的支持下添加RS232/485、USB、以太网等扩展通信手段也非常方便。数字控制的电源产品能够实现大部分数字电源的功能需求,但如果不添加一些额外部件,还实现不了全部功能需求。
这种“数字外壳”的架构存在以下问题:为了保证电源有较高的稳压精度,A/D转换器必需要有较高精度的取样,但高 精度的取样频率需要更长的A/D转换时间,造成回路的实时反应能力变差。而且,高速的采样和运算将产生巨大的运算量,能达到实时要求的核心处理器还是很少的。虽然在要求比较高的场合一般都会用DSP芯片,其运算和取样速度快,功能强大,但DSP芯片结构复杂,成本比较高;而且DSP控制技术较难掌握,对设计者要求比较高。通用DSP芯片不是专门作为电源控制芯片使用的,一般的电源应用对通用DSP芯片资源的利用率不高。不过目前以DSP为主要处理单元的数字电源芯片厂商,如TI、Freescale等公司都在优化其作为数字电源核心的DSP的结构,同时努力降低成本,并改善开发手段(提供评估板、IP模块 等),以帮助开发人员轻松地如期完成开发。除了DSP的方案,有的厂商提供基于MCU(如Silicon Labs公司)或状态机(如Zilker公司)的方案。MCU长于控制,而状态机的优点是低功耗。鉴于DSP和MCU两种方案各有长处,现在有的厂商(如 SiliconLabs公司、Microchip公司)开始将硬件DSP和辅助MCU同时集成入芯片中,使系统性能**,效率已经可以与模拟电源相媲美。
软件设计对数字电源设计人员而言是另一个挑战。为降低数字电源的设计门槛,很多半导体厂商推出了不需要软件编程或者支持图形用户接口(GUI)的数字电源解决方案,设计人员通过GUI界面就能设定电源特性参数,而不需要任何编程技能。此外,还可根据具体系统的情况,设定每个输出电压的跟踪、升压时间和延时等。有的数字电源管理芯片允许设计人员通过芯片管脚配置电源特性参数。许多数字电源芯片允许在系统运行中通过电源管理总线(PMBus)来实时更改电源输出特性。系统控制算法的设计通常是在专用的集成开发环境IDE中进行,例如TI的面向DSP的CCS、Silicon Labs的基于MCS51的IDE等。
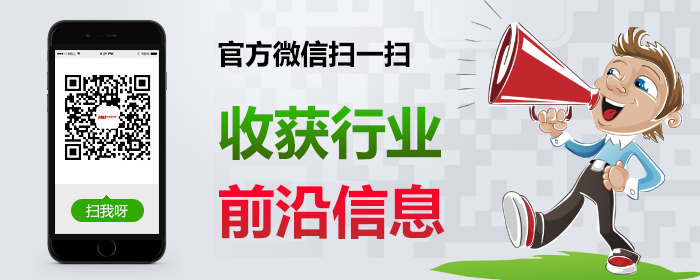