高温压力管道红外热成像检测技术研究
【摘 要】高温压力管道在石油化工厂和电站得到广泛应用,但这些管道在运行一段时间后由于介质的腐蚀和冲蚀,极易产生局部壁厚减薄并*终导致泄漏。为了寻求及早发现这些缺陷的合适的无损检测方法,建立了大型管道试验装置,并对带有不同几何尺寸内部开孔缺陷的4种不锈钢和20钢钢管进行了的红外热成像检测试验研究。试验结果表明,红外热成像检测技术是十分适用于检测高温压力管道内部腐蚀缺陷的无损方法,检测灵敏度能够满足压力管道**运行的要求。
【关键词】高温、压力管道、红外成像检测、红外检测
高温压力管道红外热成像检测技术研究
高温压力管道红外热成像检测技术研究
高温压力管道红外热成像检测技术研究
INFRARED THERMOGRAPHY TEST FOR HIGH TEMPERATURE PRESSURE PIPE
高温压力管道红外热成像检测技术研究
高温压力管道红外热成像检测技术研究
高温压力管道红外热成像检测技术研究
INFRARED THERMOGRAPHY TEST FOR HIGH TEMPERATURE PRESSURE PIPE
SHEN Gong-tian, LI Tao*, YAO Zhe-hua, QIU Hpng-cheng*
(Center of Boiler and Pressure Vessel Inspection and Research,
State Bureau of Quality and Technical Supervision of China, Beijing 100013, China)
(*Machinery Research Institute of Tianjin Petro-chemical Corporation, Tianjin 300271, China)
Abstract: High temperature pressure pipelines are extensively used in petrochemical plant and power station. The pits or wall loss defects can be severely internally produced after a certain period of time due to media corrosion and cavitation erosion. These defects finally lead to leakage of the pipes. In order to search for a good non-destructive method for these defects, a big testing installation was constructed. A serious of infrared thermography testing experiments were performed for 4 kinds of stainless steel and carbon steel pipes which are drilled different size holes on inner-surface. The testing results show that infrared thermography test is a very suitable method for non-destructive test of corrosion pits and wall loss defects of high temperature pressure pipes. The testing sensitivity satisfies the requirements of pipe safety operation.
Keywords: High temperature; Pressure pipe; Infrared thermography test; Infrared test
1 引言
高温压力管道在石油化工厂和电站得到广泛应用,并时而有泄漏和爆炸事故的发生。引起压力管道泄漏和爆炸事故的主要因素包括腐蚀、介质冲蚀、焊缝中的焊接缺陷开裂、应力腐蚀开裂、材料劣化和阀门破裂等。根据大量的事故统计,腐蚀和介质冲蚀是引起压力管道泄漏和爆炸事故的主要原因,约占总事故的50%。因此,采用有效的无损检测方法及时发现压力管道母材上由腐蚀和冲蚀引起的局部壁厚减薄缺陷,并将这些管道部位进行更换,是确保压力管道**运行的重要手段。根据检测的工作原理分析,X(或γ)射线、超声和红外热成像检测技术均适合于进行压力管道壁厚减薄缺陷的检测,而红外热成像检测技术由于具有非接触、快速区域扫描和对人无伤害的优点,在高温压力管道内部蚀坑和壁厚减薄缺陷的在线检测方面具有潜力。
注:国家“九五”科技攻关项目(96-918-0202)科研成果
材料中存在的某些异常变化可以改变材料内部的热流动状态,而热流动状态的改变必定引起材料表面局部温度的变化。无损检测中的红外和热成像方法都是利用这一基本原理,通过测量材料表面的温度变化,以推断材料内部缺陷的情况。热图形或热图像的研究称为热成像技术。
在工业设备的无损检测方面,人们主要是利用红外技术监测电气设备、动力机械设备和高温设备的运转状况,及早发现故障的隐患[1-3]。然而,在压力管道的红外检测方面,近来通过国际联机文献检索,从INSPEC(英国科学文摘)、EI(美国工程索引)、ISMEC (机械文摘)和METADEX(金属文摘)四个数据库中仅发现10多篇涉及压力管道检测的文献,但其中绝大部分为研究高温管道的保温状态及热损失[4]、换热器管的热传导效率[5-7]、复合材料管道的缺陷检测[4]和埋地水泥管道的泄漏检测[8]等。鉴于金属导热非常迅速,很少有人对压力管道母材上存在的缺陷进行检测试验研究,仅发现加拿大Maldague报道了对一小口径管道加40度热水时,采用红外热成像可以测到弯头内部两个大腐蚀坑缺陷的文章[1, 9],没有发现对压力管道内部腐蚀引起的壁厚减薄缺陷的系统研究和实际应用的报导。
本文通过建立一个大型的管道试验装置,对不同壁厚的不锈钢和碳钢管道的内部不同深度的壁厚减薄缺陷进行了加温或降温过程的红外热成像检测试验研究。
2 试验装置
2.1 TVS-2100系统
本试验采用TVS-2100红外热像系统,该系统属于光机扫描型,采用InSb探测器(10元阵列),光谱响应带宽是3~5.4μm的短红外波段,热像仪测温范围为-40~950℃,*小可探测温差(MDTD)在30℃时达到0.1℃,灵敏度0.01℃,空间视场为10。(V)×15。(H),空间分辨率为2.2mrad,测试距离大于20cm,扫描速率为30帧/秒,存盘速率为10秒/帧。红外热像仪输出标准电视信号,全部试验过程可以记录在录像带上,同时可将选定的热图像以10秒/帧的速度记录到软盘上。
对于2.2mrad的空间分辨率,其*小测试距离(0.2m)下的*小可分辨的目标为:0.44mm,热像仪与探测目标不同距离下的*小可分辨目标尺寸见表1。
表1 TVS-2100热像仪在不同距离下的*小可分辨目标尺寸
距离 (m)
|
0.2
|
0.4
|
0.6
|
0.8
|
1.0
|
1.2
|
1.4
|
1.6
|
1.8
|
2.0
|
3.0
|
4.0
|
5.0
|
10
|
*小目标(mm)
|
0.44
|
0.88
|
1.32
|
1.76
|
2.20
|
2.64
|
3.08
|
3.52
|
3.96
|
4.4
|
6.6
|
8.8
|
11.0
|
22.0
|
2.2 压力管道试验装置
选用不同规格的5段1米长的管道和两个弯头建立了压力管道红外试验装置,每段管道采用并联的方式与上下两端的总管道相连接,为试验方便每段试验管道的上下两端各安装一个阀门,整个试验装置与冷水和150℃的蒸汽管道相连接,根据试验要求可以通水或热蒸汽。试验用管道的型号如表2所示。
2.3 压力管道内部缺陷的制备
将1米长的1个不锈钢管和3个碳钢管纵向刨开成三部分,在内部制作尺寸不同的开孔缺陷,然后重新焊接成管道。开孔缺陷的大小如表2所示。
表2 4种钢管内部制造开孔缺陷列表
钢管型号(mm)
|
内部开孔缺陷数量、尺寸(mm)
|
Ф114×4 不锈钢管
|
24个:直径(Ф2,Ф4,Ф6,Ф10)X
深度(15%,25%,35%,50%,65%,75%)
|
Ф140×5 20钢钢管
|
24个:直径(Ф2,Ф4,Ф6,Ф10)X
深度(20%,40%,50%,60%,70%,80%)
|
Ф168×16 20钢钢管
|
12个:直径(Ф4,Ф8,Ф12)X
深度(10%,20%,40%,60%)
12个:直径(Ф5,Ф10,Ф15)X
深度(20%,40%,60%,80%)
|
Ф180×36 20钢钢管
|
12个:直径(Ф4,Ф8,Ф12)X
深度(10%,20%,40%,60%)
12个:直径(Ф5,Ф10,Ф15)X
深度(20%,40%,60%,80%)
|
3 现场压力管道红外热成像检测影响因素试验
3.1 太阳光及背景反射对红外热成像的影响
在常温状态下,对于不锈钢管道,太阳的照射可以产生几十度温度差异的区域,而在镜面反射角可以引起一百多度的误差,窗户反射阳光可以引起十几度的温度差异。通以150℃的蒸汽以后,阳光的照射和窗户的反射影响相对减弱,但仍然有十多度到几十度的影响。
在常温状态下,对于带防锈漆的碳钢管道,太阳的照射可以产生几十度温度差异的区域,窗户反射阳光可以引起几度的温度差异。如图1所示,1(a)为将阳光遮挡时的热图像,管道本体的温度只有8℃,1(b)为管道装置附近玻璃窗反射太阳光到管道上测试的热图像,阳光照射部位管道上的显示温度为15℃,1(c)为太阳光直接照射到管道测试的热图像,阳光照射部位管道上的显示温度为75℃。通以150℃的蒸汽以后,窗户的反射对热像图无影响, 阳光的照射影响相对减弱,但仍然有十几度的影响。
在常温状态下,对于表面均匀氧化腐蚀的碳钢管道,太阳的照射可以产生几度温度的整体差异,而窗户反射阳光已观察不到影响。通以150℃的蒸汽以后,阳光的照射影响已观察不到。
在常温状态下,对于表面不均匀氧化的碳钢上弯头,太阳的照射可以产生十几度温度差异的区域,而窗户反射阳光已观察不到影响。通以150℃的蒸汽以���,阳光的照射影响已观察不到。
3.2 管道表面状态对红外热成像的影响
经试验发现,管道的不同表面状态会具有不同的红外辐射率,而红外仪器只能设置为一个辐射率,由此不同辐射率的材料在同一温度下,在热像仪上可以测到不同的温度,如图2所示,为Ф89×1000×2碳钢管通以150℃蒸汽后的热图像,由于上部为红色防锈漆,发射率为0.97,下部为银色防锈漆,发射率为0.75,因此在热像仪设置发射率为0.97的情况下,产生的热图象两部分的温度为20℃。
4 带缺陷压力管道的红外热成像试验
4.1 直接通蒸汽加热试验
直接加热试验为在室温下,对试验管道直接通以150℃的蒸汽,以热像仪观察和记录管道升温过程中内部缺陷的热图像。4种钢管在升温过程中内部缺陷典型的热图像如图3~图6所示。表3为4种钢管可检测到*小缺陷的统计表。
表3 4种钢管可检测到*小缺陷统计表
钢管型号
|
可检测*小内部开孔缺陷尺寸(mm)
|
Ф114×4 不锈钢管
|
Ф10×15%,Ф6×25%,Ф4×50%,Ф2×65%
|
Ф140×5 20钢钢管
|
Ф10×20%,Ф6×40%
|
Ф168×16 20钢钢管
|
Ф10×20%,Ф8×20%,Ф5×40%
|
Ф180×36 20钢钢管
|
Ф12×20%,Ф10×40%,Ф8×60%
|
4.2加热后外部冷却试验
管道通以150℃蒸汽加热达到热平衡后,采用冰块和制冷气体对管道表面进行冷却,在冷却后瞬间,对于Ф114×1000×4不锈钢管,可以测试到内部大于Ф6×1.0的开孔缺陷;对于Ф140×1000×5碳钢管,可以测试到Ф10×2.0的内部开孔缺陷。图7为钢管通以150℃的蒸汽后,用冰制冷瞬间内部开孔缺陷产生的热图像。
5 试验结果分析
通过对红外热成像试验过程进行观察和对表3所给出的试验数据进行分析,可以发现如下一些现象和规律:
1) 将Ф114×4不锈钢管红外热成像可检测到的*小开孔缺陷与Ф140×5碳钢钢管可检测到的*小开孔缺陷比较发现,不锈钢的检测灵敏度比碳钢高得多,而且针对Ф10的开孔而言不锈钢缺陷从出现到温度平衡的可观测时间为2分钟以上,而碳钢管缺陷从出现到温度平衡的可观测时间仅为30秒左右,纠其原因是因为不锈钢的导热系数约为15W/(m.℃),碳钢的导热系数约为48W/(m.℃)。即材料的导热率是影响检测灵敏度的关键因素之一,导热率越底,检测灵敏度越高,缺陷显现的时间越长。
2)对于同一个钢管不同孔径的缺陷,可观测到的缺陷深度不同。这一现象说明,缺陷的几何尺寸是影响对红外热成像检测灵敏度的另一关键因素,缺陷面积越大,可检出的壁厚减薄量的灵敏度越高,面积越小,灵敏度越底。
3) 对于3种不同厚度的20钢钢管进行比较,壁厚越薄,可检测缺陷的几何尺寸也越小,但壁厚越厚,缺陷可观测的时间越长,对于Ф10的开孔,Ф140×5钢管缺陷从出现到温度平衡的可观测时间仅为30秒左右,Ф168×16钢管缺陷从出现到温度平衡的可观测时间约为120秒,Ф180×36钢管缺陷从出现到温度平衡的可观测时间约为200秒。由此可见,材料的厚度也是影响灵敏度的关键因素,材料越厚检测缺陷的灵敏度越底,但缺陷的可观测时间越长。
4) 将内部进行加热和外部进行冷却的试验结果相比较,采用内部加热法可检测缺陷的灵敏度高于外部冷却法,采用制冷气体冷却的灵敏度高于采用冰冷却的灵敏度。
5) 将表2所列的4种钢管按内部工作压力为3MPa为工作条件,采用断裂力学进行计算,得到所有这些管道上直径为10mm减薄为80%壁厚的蚀坑或开孔的强度是**的,因此采用红外热成像检测的灵敏度,大大超过了管道**运行可允许缺陷的要求。
6 结论
(1) 试验结果证明,红外热成像检测技术是高温压力管道内部腐蚀和冲蚀缺陷的可靠无损检测方法,该方法检测出的*小缺陷尺寸,大大超过了管道**运行可允许缺陷的尺寸,满足管道的检测要求。
(2) 材料的导热率是影响检测灵敏度的关键因素之一,导热率越底,检测灵敏度越高,缺陷显现的时间越长。
(3) 缺陷的几何尺寸是影响对红外热成像检测灵敏度的关键因素之二,缺陷面积越大,可检出的壁厚减薄量的灵敏度越高,面积越小,灵敏度越底。
(4) 材料的厚度也是影响灵敏度的关键因素之三,材料越厚检测缺陷的灵敏度越低,但缺陷的可观测时间越长。
(5) 温度激励方式是影响检测灵敏度的关键因素之四,采用内部加热法可检测缺陷的灵敏度高于外部冷却法,采用制冷气体冷却的灵敏度高于采用冰冷却的灵敏度。
参 考 文 献
[1] Xavier Maldague, Nondestructive Testing Monographs and Tracts Volume 7, Infrared Methodology and Technology [M], Gordon and Breach Science Publishers, 1992.
[2] Roderic K. Stanley, Patric O. Moore and Paul Mclntire eds, Nondestructive Testing Handbook, Volume 9, Special Nondestructive Testing Methods [M], American Society for Nondestructive Testing, 1995.
[3] T.-M. Liou, C.-C. Chen, T.-W.Tsai, Heat transfer and fluid flow in a square duct with 12 different shaped vortex generators [J], Transactions of the ASME. Journal of Heat Transfer May 2000. Vol.122, no.2, p327-335
[4] Richard N. Wurzbach, David A. Seith, Infrared Monitoring of Power Plant Effluents and Heat Sinks to Optimize Plant Efficiency [A], Proceedings of SPIE [C], The International Society for Optical Engineering Thermosense XXII,April 24-27, 2000, Orlando, FL, USA.
[5] R. Rozenblit, M. Simkhis, et al, Heat Transfer in Horizontal Solid-liquid Pipe Flow [J], International Journal of Multiphase Flow, 2000,Volume 26, No.8.
[6] Shigemichi Yamawaki, Toyoaki Yoshida, et al, Fundmental Heat Transfer Experiments of Heat Pipes for Turbine Cooling [A], American Society of Mechanical Engineers (Paper) Proceedings of the International Gas Turbine & Aeroengine Congress & Exposition [C],June 2-5, 1997, Orlando, FL, USA.
[7] Yuwen Qin, Naikeng Bao, Thermographic Nondestructive Testing Technique for Delaminated Defects in Composite Structure [A], Proceedings of SPIE [C],The International Society for Optical Engineering Thermosense XVII, 1995, Orlando, FL, USA.
[8] Kenneth R. Maser, Mehdi S. Zarghamee, Proceedings of the Speciality Conference on Infrastructure Condition Assessment [C], August 25-27, 1997, Boston, MA, USA.
[9] Xavier Maldague, Pipe Inspection by Infrared Thermography [J], Materials Evaluation, 1999,Volume 57, No.9.
版权所有 Copyright(C)2011 武汉市富运达光电有限公司
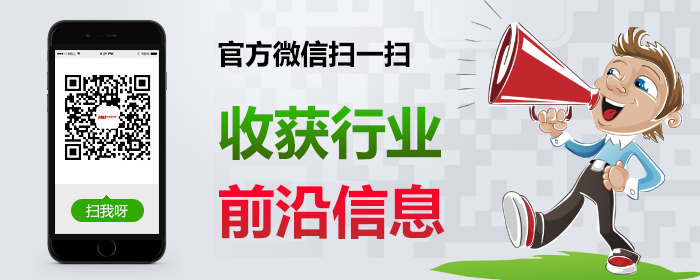