应用SPC技术监控和评估饮料瓶清洗卫生数据-ATP荧光检测仪技术文章
应用SPC技术监控和评估饮料瓶清洗卫生数据-ATP荧光检测仪技术文章
应用SPC技术监控和评估饮料瓶清洗卫生数据-ATP荧光检测仪技术文章
在冷装饮料生产加工系统中,瓶子残渣和卫生情况是一项非常重要的。不像“热装”饮料生产加工系统那样,在“热装”操作中瓶子就同时被**了,“冷装”系统并不是这样的。因此,用来装饮料的瓶子需是完全干净的以防止或*小化对成品的再污染,这是非常重要的。
关键的是引入“不清洁”的塑料瓶可能携带令人不满的污垢和对成品的再污染的**,因此这可能会在产品的**和保质期方面有反作用。即使瓶子经过清洁处理,它仍可能包含可能引起成品反面影响的微生物负载量。因此,洗瓶后的微生物对成品的**卫生至关重要。
我们的研究目的在于通过运用SPC的技术,来分析微生物数据,从而建立一个趋势分析的系统,这样一来,我们就可以得到一个控制点的预警信息,而不是仅仅判定控制点的状态是否正常。
为了确保所选用的SPC图表使用于对过程的研究,事先应对过程的可靠性进行评估以保证过程受控。研究中发现,当过程的可靠性指数CPK的值为1.00时,表明该过程是受控的。在此阶段,由非随机原因造成的偏差在可能情况下应被消除。
方法;
研究中的清洗瓶的微生物数据从某饮料厂获得。控制点为清洗后的瓶子,每次生产过程中都要测量控制点,对三个月收集的数据加以分析,用来建立起合理的趋势分析方法。
因为这些**总数数据是自然分组的计量数据,对于得到的数据,应用均数—极差控制图进行处理和分析。
结果:
三个月来清洗瓶控制点的**总数数据显示在表1中。从表中无法发现这520个**总数数据有任何异常。
经过统计处理,52批次清洗瓶**总数的均数控制图,见图2,在均数控制图中,由于第49,50组清洗瓶**总数的均数均在C区,因此,显示在第51组出现异常。(根据GB/T4091-2001标准的常规控制图判异检验模式五)
均数控制图中:CL =16.46 UCL=27.60 LCL=5.32
在这里,均数控制图清晰的给出了预警信息,预示第51批会出现偏差。换句话说,如果在第50 批或更早实施必要的纠偏措施完全可以预防这个偏差的出现。
讨论:
HACCP体系中*基本的理念就是预防,SPC也是如此。将两者结合,必然会增进这一理念。在这案例中,用的是趋势分析方法。
在这次研究中,趋势分析是采用了回顾调查的方法。它不可能找出第51批出现偏差/异常的诱因。然而,在实时监控的情况下,通过与工作程序控制的结合,在第51批就应调查引起**总数均数异常的理由。无论是否非随机或随机原因所致。非随机的原因可能是:**水配置浓度有误、瓶子的污染、检验的失误、结果误读等,随机的原因可能是:**水浓度自然降低、操作员工的系统误差。通过不断消除可能造成偏差/异常的原因,出现偏差/异常的控制点就会减少。
传统的微生物分析方法的弊病在于时效性差,往往是产品已经在超市货架上销售了,但分析还没完成。SPC的技术为食品生产提供了实时的控制工具,为管理者提供了危害和偏差的预警。
本文的主要目的在于展示将SPC应用于HACCP卫生数据分析中的潜在好处。为了更**的评估其作用,建议更多的研究*好在现场即时的环境下进行。
结论:
应用SPC的两个图表来分析HACCP体系中一个控制点的微生物数据,可以更好地得到数据的趋势情况。这项技术不仅仅反映出控制点状态是否正常,还会将预警信号显示在图表上,以便管理者采取必要的纠偏措施,防止偏差危害的产生。SPC可使HACCP卫生管理系统更为有效,从长远来看,对生产效率的提高也非常有益。
转自食品伙伴网
转自食品伙伴网
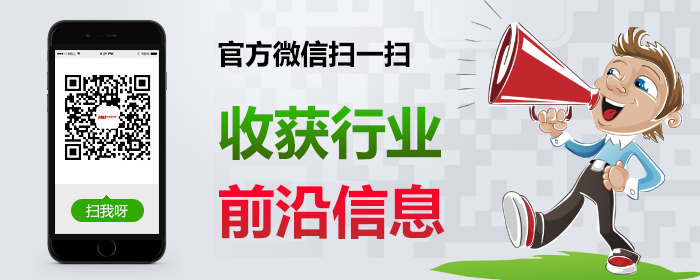