ADEV埃登威氧化锆氧分析仪**氧化锆氧分析技术的*新进展
电化学传感器气体分析技术在控制能源和原料消耗、改善工业过程生产率以及控制污染物排放等工业领域,正在发挥日益重要的作用。事实上,汽车工业早已开发出各种固态传感器,用于汽车发电机燃烧效率控制。目前,**于汽车工业的这项检测技术已将应用领域拓展至工业窑炉、锅炉和汽轮机等 。
如今,氧化锆氧量传感器广泛应用于各种工业领域和运输工具。上世纪70年代初期,在钢铁生产控制中**采用了一次性氧化锆氧量传感器,分析铁水中的氧含量。上世纪60年代,为了开发固态氧燃料电池(SOFC),研制出坚固耐用的铂电极和固态氧化锆电解质(氧化锆结晶体)。其后,美国西屋电气公司在此基础上,开发出**台用于过程气体分析的工业用氧化锆氧量传感器。时至今日,氧化锆氧量传感器的主要应用仍然集中在控制汽车发动机的空气/燃油比
在空气与燃油混合点火时,要求空气要达到一定的比例,以期使燃烧过程完全充分。燃烧后废气中的氧含量可以直接反映燃料混合物中空气量的相对富裕或相对不足。自上世纪70年代起,氧化锆氧量传感器,或称为λ传感器,一直用于监视汽车废气中的氧含量。
在空气与燃油混合点火时,要求空气要达到一定的比例,以期使燃烧过程完全充分。燃烧后废气中的氧含量可以直接反映燃料混合物中空气量的相对富裕或相对不足。自上世纪70年代起,氧化锆氧量传感器,或称为λ传感器,一直用于监视汽车废气中的氧含量。
1976年,受普通火花赛设计的影响,德国博世公司**在其不加热的锥管型λ传感器(LS)中,装入了氧化锆传感器本体,用于汽车发动机的反馈燃油控制。不加热的氧化锆氧量传感器仅仅依靠废气的热量,使工作温度达到600-900℃。
1982年,德国博世研制了**代加热的锥管型λ传感器(LSH),目的是减少冷启动时的废气排放。
1997年,德国博世又开发了加热的平面型λ传感器(LSF)。LSF传感器由铂电极、固态氧化锆电解质(氧化锆结晶)、绝缘材料和加热器组成,采用分层结构,叠压在薄形基片上。
*新型的氧化锆传感器技术是基于平面型λ传感器设计,具有直接测量空气/燃油比的功能。以往所有的λ氧传感器均采用传统的来回切换式设计。*新的宽带式λ传感器(WB)则完全摒弃了这种设计理念,可以产生与空气/燃油比成正比的信号。
宽带式氧化锆传感器与锥管型或平面型传感器的相同之处在于:当空气/燃料比中的空气量相对不足时,产生一个低电压信号;当空气量相对富裕时,产生一个高电压信号。不同之处在于:宽带式氧化锆传感器没有快速的切换动作,而是根据空气/燃料比中空气量的相对富裕或相对不足,缓慢地增加或减少电压。在*佳空气/燃料控制比14.7:1位置,宽带式氧化锆传感器会产生稳定的450mV电压信号。若空气量出现微小的相对富裕或相对不足时,传感器的输出电压也相应地产生微小变化,而不是剧烈地增加或减少。宽带式氧化锆传感器的另一个不同之处在于加热器电路。与平面型传感器一样,宽带氧化锆传感器的加热器电路也是印制在陶瓷片上,但是采用脉冲持续时间模块化设计,使工作温度稳定在700-800℃范围内。BOSCH的宽带式λ传感器,即LSU 4.9,对空气/燃油混合物变化的响应时间小于0.1秒,其内部加热器可以使传感器的工作温度在20秒内达到800℃。
氧气泵是宽带式氧化锆传感器的组成部分。为了**测量,氧气泵抽取被测排放气体,注入到电化学电池组(称为能斯特电池)之间的“扩散”间隙。能斯特电池用导线与氧气泵连接,根据“扩散”间隙中的氧含量,能斯特电池分流一部分电流。当电流值达到动态平衡时,其与被测排放气体中的氧含量成正比,该信号可以为发动机的计算装置,提供**的空气/燃油比,从而满足国际*新的汽车排放标准。
氧化锆传感器开发的另一个重要里程碑,是由意大利ADEV埃登威率先引入了焙烧铂金属陶瓷电极技术和釉底料技术。所谓的釉底料技术是将多孔保护膜与等离子喷涂晶体层技术相结合,形成双保护层系统 尽管用于汽车工业排放控制的λ传感器非常先进、可靠,但还是很难适应在线工业过程的应用要求,问题的主要症结在于严酷的工作环境和传感器的封装材料。
2. 理论基础
所有工业用氧化锆传感器均基于以下原理:电池由固态氧化锆电解质(绝大部分为稳定的氧化钇?氧化锆,简称YSZ)和两个铂电极所组成。铂电极焙烧在氧化锆陶瓷片的两侧,暴露在被测过程气和参比气中:
O2(参比侧氧分压),铂电极 │ 氧化锆 │铂电极,O2(测量侧氧分压)
使用高温密封材料和氧化锆陶瓷片,使测量侧与参比侧彻底分离。由于氧化锆传感器两侧的氧浓度不同,形成浓差电势E,该电势大小符合能斯特方程: 式中,
C为常数,与氧化锆锆头的热接点、参比侧与测量侧的温度和压差有关;R为通用气体常数;T为被测过程气的温度,单位K;F为法拉第常数。
氧反应发生在“三相区域”(简称TPB,即铂电极、固态氧化锆电解质和被测气体),其中, O2代表氧分子;e’代表电子;VO”代表氧离子空穴(请参阅图1A)。氧反应过程包括:氧分子吸收、电解质/电极表面分解、以及*后扩散至TPB,在TPB处发生氧电化学反应。如果使用复合的离子-电子导电电极,或者带电子和离子导体的陶瓷电极(例如:铂-氧化锆),则在电极主体发生氧电化学反应,这样可以有效改善氧传感器的使用性能(请参阅图1B)。
O2(氧气)? O2(电解质 / 电极)
O2(电解质 / 电极)? 2O(电解质 / 电极)
2O(电解质 / 电极)? 2O(电解质 / 电极 / 被测气体)
2O(TPB)+ 4e’(电极)+ 2VO”(电解质)? OO(电解质)
图1. 氧传感器电化学反应
通常,在参比侧固定氧分压,例如,空气压力p(O2)=0.21bar时,热平衡型氧传感器上的信号只取决于过程和/或传感器加热器温度。
工业氧化锆氧量传感器通常工作在300℃以上的温度条件下,氧离子在氧化锆传感器中迁移,并*终在氧化锆的测量侧、参比侧和氧化锆电解质表界面实现氧平衡。提高工作温
度可以改善传感器的性能,但是,高温对传感器的封装材料是一个极大的挑战。因此,绝大多数工业用氧化锆氧量传感器的工作温度在700-800℃范围内。
3. 氧化锆锆头设计
工业用氧化锆氧量传感器的有两种设计结构,一种是密闭的锆管结构,另一种是将盘状锆池封装在铝质或其它金属锆管上的结构(参阅图3)。
图3. 氧化锆锆池示意图
锆管结构或“套筒式”工业设计,具有良好的使用性能,但是,由于锆池陶瓷组件带凸缘结构,形状较为复杂,且整个锆管均受到热应力的影响,因此,该氧化锆锆池的强度较差。此外,锆池中的电化学反应区域的热平衡也不能达到*佳状态。
盘状锆池封装在金属锆管上的结构,由于金属盘和金属锆管的热膨胀系数完全匹配,因此,参比侧与测量侧之间的温差很小,氧化锆陶瓷组件所受的热应力影响也很少。此外,独特的多孔铂-氧化锆陶瓷电极组件设计,拓宽了发生氧反应的TPB界面,改善了氧传感器的响应时间和使用寿命。
工业用氧传感器的*高品质规格是工业在线应用,即要求氧化锆氧量传感器即使是在极端温度和爆炸性环境,也能可靠地工作多年(请参阅图6-7)。
图6. ZR202G氧分析仪(日本横河)
图7. X-STREAM 氧分析仪(Rosemount Analytical)
Inconel、哈氏合金或316L不锈钢属于特种合金,在高温过程环境条件下,具有优异的抗氧化和抗腐蚀性能。可以使用上述合金制做氧化锆锆管、内部标定气管线和参比气管线(请参阅图8)。
图8. X-STREAM O2氧化锆锆头组件
特制的氧化锆锆池组件可以改善热平衡,陶瓷或金属扩散元件适用于含高粉尘的测量应用。这两个特性均可以提高氧分析仪的性能(请参阅图9)。
4.用氧化锆分析仪监控燃烧过程
工业用氧化锆分析仪广泛用于燃烧过程的监测与控制,应用范围包括耗能行业(钢铁、电力、石油化工、陶瓷工艺、纸浆造纸、食品、纺织)和各种燃烧设备(锅炉或焚化炉等)。*佳的燃烧状态要求烟气中CO2含量应达到*大值,O2浓度则应接近于零。
在*佳燃烧状态,氧气和燃料的配比应符合理想比例。通常,烟气中的主要成分是二氧化碳CO2和水H2O。此外,还有极少量的其它气体,如二氧化硫SO2和氮氧化物NOX,这些气体来自于燃料杂质和空气中的氮气被氧化。
理想的化学计量点——*高效率和*低排放,在实际燃烧过程中是无法实现的,原因是燃料/空气的配比、燃能密度、燃料和空气流量都不是一成不变的。氧化燃烧过程会造成热量损耗,并产生大量的氮氧化物污染;还原燃烧过程燃烧不完全的燃料,通过烟囱会排放大量煤烟,造成环境污染,同时极大地缩短燃烧器的使用寿命。此外,由于燃料、空气不可能完全混合,因此,理想燃烧实际上是不可能实现的,绝大多数燃烧设备烟气氧含量均控制在几个百分点。通常,燃气燃烧器烟气氧含量控制在2-3%;锅炉和燃油燃烧器烟气氧含量控制在为2-6%。烟气温度越低,燃烧效率越高。
一般来说,氧含量控制在0.75-2%,燃烧可达到*佳状态。不同的烟气温度,燃烧过程氧含量每减少1%,可节约燃料1-3%。
与燃气 或燃油锅炉不同,燃煤锅炉的烟气含有大量粉尘,如:飞灰、硫和二氧化硫SO2等。众所周知,抽取式的分析系统存在堵塞和冷凝问题,与之相比,直插式O2/CO测量技术就显示出较高的可靠性。
单独测量烟气的氧含量可以较好地控制燃烧过程,如果同时再测量一氧化碳CO,则可以进一步提高燃烧效率和控制稳定性。经验证明:若烟气中含有约100ppm的一氧化碳和少量的氧,则燃烧过程可以接近化学计量点,达到*高的燃烧效率。燃煤电厂锅炉平均的O2/CO浓度测量示例
用氧化锆分析仪监测氧和一氧化碳,控制燃烧过程,对降低氮氧化物NOX和二氧化硫SO2排放也是有效的。因为同时监测两个参数,可以控制燃料燃烧更完全,使燃烧过程接近于化学计量点,燃烧效率*高,此时氧含量控制在1-2%。
燃烧过程中,烟气温度是变量,氧化锆分析仪可以在检测氧含量的同时,观测到烟气温度的变化。在烟气温度变化过程中,为了使氧含量测量更准确,信号更稳定,要求氧
化锆分析仪要能够保持热平衡,以消除热接点对氧测量信号的影响(市场上有些氧化锆分析仪,温度的波动影响达到10mV,对氧测量信号的影响为3±1%O2)。
烟气温度变化对Rosemount Analytical的X-STREAM氧化锆分析仪的斜率和常数影响极小当被测过程温度在25-600℃范围内变化时,由此产生的氧含量测量误差小于±0.025%O2(请参阅图14)。这一新型的工业用氧化锆分析仪可以在较宽测量范围内,保证氧含量测量的稳定性和**度。但是,不包括在空气中测量,因为空气湿度的变化会影响氧分压,而传感器的测量信号与氧浓度成对数关系,因而会给传感器引入比较可观的测量误差
实时控制可以有效地改善现代燃烧控制过程。一般情况下,燃烧控制过程可以分成两类:操作点控制(OPC)和有效燃烧控制(ACC)。
在有效燃烧控制ACC中,控制器的输出用于调节流量特性,例如调节燃料流量。ACC已经在许多分层火焰燃烧炉和紊流燃烧器中取得了不同程度的业绩。贫燃料预混燃烧可以降低火焰温度,因而是减低NOX排放的有效方法。但是,这种方法有两个缺点,一是熄火,二是控制稳定性不好 [2]。在这种控制应用中,要求氧化锆传感器必须能够迅速、**地确定燃烧系统的工作状况。燃烧不稳定的情况是经常发生的,其发生频率小于500Hz,故在这种控制应用中,要求传感器的实时响应频率要达到kHz级,这样才能提供有效的反馈控制信号。
操作点控制(OPC)是通过调节燃料注入量,控制火焰参数。这种控制没有**的空气流量信息,只是基于实际的火焰特性和估计的空气流量进行控制。在这种控制应用中,可以利用氧化锆传感器的测量结果,**地调节燃料/空气比。
有关氧化锆氧量传感器的材质、在不同环境中传感器的使用性能和应用限制等更多详细信息,可以参阅*近发表的相关资料。
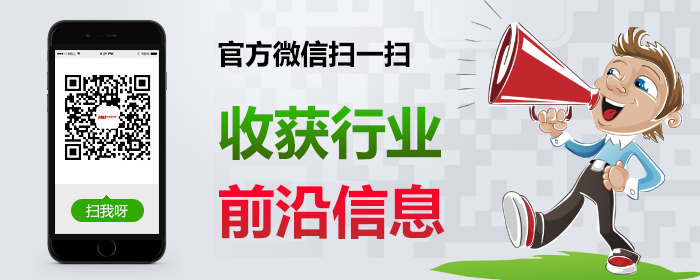