干法水泥工艺知识
一、概况
宁国水泥厂拥有两条干法生产线,一线是国家“六五”计划重点工程之一,年产熟料120万吨,年产水泥129万吨(普硅104万吨,纯硅25万吨),投资4.62亿元。1982年6月完成三通一平,9月破土动工,1985年3月31日原料磨进行试生产,4月21日回转窑投料试生产,4月30日水泥磨进行试生产,11月24日至1986年5月26日期间进行引进设备的性能考核(先单机后全厂),6月21日中、日双方正式交接验收签字,7月1日正式投产。
二线于1995年4月28日破土动工,1996年10月18日**次点火,1996年12月31日投料试生产,1997年4月26日实现达产、达标。
二、基本概念
1、水泥:凡细磨成粉末状,加入适量水后成为塑性浆体,既能在空气中硬化,又能在水中硬化,并能将砂、石等散粒或纤维材料牢固地胶结在一起的水硬性胶凝材料。
2、胶凝材料:凡能在物理、化学作用下,从浆体变成坚固的石状体,并能胶结其它物料而具有一定机械强度的物质。
3、硅酸盐水泥:凡由硅酸盐水泥熟料、适量石膏磨细制成的水硬性胶凝材料。随着混合材掺加量的不同而得出不同的水泥。(活性混合材掺量≤15%,非活性混合材掺量≤10%)
4、有关熟料的基本概念
⑴、矿物组成:C3S、C2S、C3A、C4AF,其中C3S+C2S:70~75%,(硅酸盐矿物)C3S:45~65%,C3A+C4AF:19~22%(熔剂性矿物)
⑵、化学组分:CaO、SiO2、Fe2O3、Al2O3
⑶、熟料率值:
① kH:用来表示CaO与SiO2结合形成C3S的程度(一般0.80-0.95,本厂:0.91±0.02,kH高,强度高);
② SM:熟料中硅酸盐矿物与熔剂性矿物的比例(一般2.4±0.2,本厂:2.5±0.1);
③ IM铁率:熟料中Al2O3与Fe2O3含量的质量比(一般1.5-2.5,本厂:1.5±0.1)。
三、生产工艺流程
现以干法一线为例进行介绍生产工艺流程。
干法一线的主要生产工艺是从日本三菱重工引进的具有七十年代末期国际先进技术装备水平的带MFC分解炉的新型干法窑外分解窑。成套生产设备由工业电视、自动化仪表、电子计算机通过中控室进行集中控制,矿山、装运以及供电、供水均采用国内配套设备。矿山配备了从德国进口的回转钻。现将制造分厂的“两磨一烧”的生产工艺流程介绍如下:
1、生料制备系统
该系统采用一台Φ5×15.6m中卸磨(0309,闭路循环烘干兼粉磨系统)。混合料、铁粉、校石按照一定的比例由皮带秤计量入磨,出磨生料粉由0315斜槽、0317斗提、0318斜槽送至0320离心式选粉机(立式,Φ7.5m)进行筛选,粗粉返回磨内,成品经0331斜槽,由0401气力提升泵(Φ2×5m,后来于1998年改为胶带式斗提机,气力提升泵作为备用线)送至两座0410生料库(Φ18×45m,11000吨/座)进行储存和均化。出磨气体由0324粗粉分离器(Φ7m)进行分离,含尘气体由2台0325旋风式收尘器收尘(Φ6m),然后由0327风机(920kW×1000r/min)排入0630立筒型气体混合室(Φ7.0×21.35m),经0604电收尘器(卧式,4个电场,能力:356470Nm3/h,风温:110℃,正压操作)处理后排入大气。
2、煤粉制备系统
该系统采用一台Φ3.4×8.75m风扫式球磨机。原煤主要由2256取料机供应(取料机故障时由联合储库皮带输送系统提供),经皮带送入0801磨头仓(130吨),经0802圆盘喂料机、0803双道锁风阀后入磨(0804)进行烘干粉磨。出磨半成品由0812粗粉分离器(Φ3.5m)分离,粗粉由0814绞刀返回磨内,含尘气体由0815旋风式收尘器(Φ2.7m)进行**收尘,成品由0816分格轮送入0820煤粉仓(Φ5.2×9.25m,60吨),出0815气体由0620电收尘器(卧式,2个电场,能力:49270Nm3/h,风温:85℃,正压操作)进行二次收尘,收集的煤粉由0830绞刀送入0820煤粉仓内储存,供窑、炉煅烧之用。
3、熟料煅烧系统
出库生料经库底0413回转滑板、0414计量滑板、0415斜槽、0417①链式斗提、0417②斜槽、0419标准仓(64m3)后,通过0423皮带秤(2.4×8m)计量喂料,由0428气力提升泵(Φ2×7m)将生料粉送至0501预热器系统进行热交换(在连接管道内进行热交换,在旋风筒内进行分离),在0507MFC分解炉(Φ6×16.5m)内进行碳酸盐(CaCO3和MgCO3)分解,在0511回转窑(Φ4.7×75m)内完成水泥熟料的烧结反应(C2S+C→C3S)而形成熟料。在此说明:原窑用三通道燃烧器于1998年元月份大修中,将其改为PLD四通道型式,进一步延长了窑内耐火材料的使用周期,提高了系统的稳定性和运转率。1400℃左右的出窑熟料进入0528篦冷机进行风冷却(1999年元月18~2月7日大修期间将一段采用德国BMH公司技术改为空气梁形式)。冷却熟料的热风分为四部分:①一室风主要作为入窑二次助燃风(1200℃);②二、三室风主要作为入炉三次风(900℃左右)促进分解炉内煅烧;③四、五室风主要作为入AQC锅炉的热源进行余热发电(350℃左右);④六、七室风属于低温风(200℃左右)经0537电收尘器处理后,由0538风机排入大气。出篦冷机的熟料被冷却至150℃左右后,由0701裙板机、0704链式斗提、0705和0706裙板机分别送入4个熟料库0707(Φ18×32m)进行储存。
4、水泥粉磨系统
出0707熟料库的熟料由0710和0711皮带、0712斗提送至0901磨头仓(210t),与矿渣、石膏按一定的比例搭配入0915水泥磨(Φ4.5×12.96m),出磨半成品经0922斜槽、0924链式斗提、0925和0926斜槽后,入0928旋风式选粉机(Φ5m 8×Φ1.8m)进行筛选,粗粉返回0915磨内;含尘气体由0935袋收尘器(脉冲式,能力:1800m3/min,气体温度90℃,总过滤面积为960m2)处理;成品由0939拉链机、1001双仓泵(120t/hΦ2.5×水平392m+垂直50m+7个90°弯头)送至8个1005水泥库(Φ18×40m,10000吨/座)内进行储存(1001双仓泵水泥输送系统技改于2001年2月份开工,7月1日设备安装结束,之后进行单机调试和部分改进,11~`15日进行接口并投入运行,自该系统改为皮带+斗提+斜槽输送的方式投入运行后,故障率大大下降,运转率和台时明显提高,水泥工序电耗由45→40kW.h/t)。出磨气体由0932粗粉分离器(Φ2.2m)进行分离,粗粉入0924斗提,含尘气体由0933袋收尘器(脉冲式,能力:600m3/min,气体温度100℃,max为130℃,总过滤面积为320m2)进行收尘处理,成品入0939拉链机。
5、矿渣烘干系统
该系统采用两台Φ3×20m烘干窑,一台Φ1.7×2.5m风扫式煤磨进行煤粉制备。采用顺流烘干,电收尘器处理窑废气,成品储存在矿渣库内(1000吨)。
四、主机设备
1、原料磨:闭路循环烘干兼粉磨的中卸磨,分为四个仓,磨机筒体由钢板卷制而成,两端装有带空心轴的磨头,磨内壁设置衬板,并装有不同规格的研磨体(钢球和钢段,本厂为钢球)。磨机转动时,钢球由于惯性离心力和摩擦力的作用,钢球产生抛落运动和滑动,物料由于破碎和研磨的作用而被粉碎,出磨物料通过筛分系统,将合格品入库,不合格品入磨再进行粉磨。
2、生料入预热器提升系统:采用的是0428气力提升泵输送系统,提供动力的是0429罗茨风机,因为该设备出口逆止阀原设计是靠0429自身产生的压缩气体将其吹起,这样,就消耗了部分的压缩空气。1995年,经过技术人员的现场考查和充分论证,将出口逆止阀的动作改为汽缸执行机构,使窑喂料量由270→290t/h;同时,于1999年将0429的主动轮进行了适当的改大,减少进气量,提高风机风压,为回转窑的提产创造了条件。为了进一步挖潜回转窑烧成系统的产能,计划在2002年将该系统改为胶带斗提+斜槽的输送型式。
3、预热器:采用的是伯利鸠斯**的四级多波尔型悬浮预热器系统,具有较低的压力损失,Ⅱ级旋风筒采用单独设置的目的:为了预热器两列的物料和热交换的平衡;另外,由于两Ⅰ级旋风筒的出风口是由切线方向对称进入Ⅱ级旋风筒的,因此,加强了料、气的搅拌程度,提高了热交换效率。
4、分解炉:若开窑投料时,物料不经过分解炉的形式称为离线式分解炉,若物料经过分解炉的形式称为在线式分解炉。本厂采用的是离线式三菱公司开发的**代MFC型沸腾式分解炉系统(H/D=2.8)。
⑴工艺布置:分解炉系统工艺布置如附图所示:Ⅱ级旋风筒收集的生料,经分料挡板分成两路:一路可以入MFC分解炉进行受热分解,一路可以直接喂入窑尾上升烟道,在上升烟道与分解炉、窑内来的气料回合流进行会合,之后进入Ⅰ级筒生料经收集入窑煅烧。开窑投料之初分料挡板全关,生料不经过分解炉,主要在回转窑内进行碳酸盐分解,即所谓的SP窑运转状态,一般SP窑(任何情况下)运行时间在2~4h为宜,否则主烧成带耐火砖易出现高温,甚至会出现“红窑”现象;当分料挡板全开,生料主要在分解炉内进行碳酸盐分解,即所谓的NSP窑运转状态。
⑵分解炉结构:MFC分解炉主要由炉体、空气室、流态化空气喷嘴、废气排出管道、三次风管、喷煤管、生料管和排渣管道组成。本厂分解炉有效规格尺寸为Φ6×16.5m,流化床面积为28.3m2。
⑶分解炉的优点:
①热交换效率高,燃烧稳定,层内温度分布均匀且稳定,没有局部高温,燃料与生料在“沸腾”床进行燃烧和分解(CaCO3→CaO+CO2↑)。
②生料在炉内停留时间长,可在还原气氛下操作,可以采用劣质煤进行煅烧。在1995年8月23日南化进行的热工标定中,测出MFC系统(含MFC炉体、炉出口斜烟道和汇流管)平均停留时间为109.7秒,可以采用“两步分解到位”的模式。
③具有显著的缓冲作用:出炉料流稳定,由于炉内流化层的作用,流化层越厚则缓冲作用越强。
⑷分解炉的缺点:
①需增设流态化风机:不断增加了工序电耗,而且使工艺流程复杂。
②炉内流化床杂物清理难度大:当炉内耐火材料产生剥落或损坏后落入炉内,流化床仅有一个Φ200mm的清渣溜管,故清理难度大。
③工艺结构复杂,操作较复杂。
五、熟料煅烧过程
1、干燥:生料中自由水蒸发过程,100~150℃,物理过程。
2、预热:生料中粘土质矿物化合水的分解过程,100~600℃,化学过程。
3、分解反应:生料中MgCO3、CaCO3在煅烧过程中分解放出CO2的过程,600~1000℃,化学过程:
MgCO3→MgO+CO2↑(590℃)、CaCO3→CaO+CO2↑(890℃)
以上两反应属于可逆反应,受分解温度和CO2分压影响。为了使反应顺利进行,须保持较高的反应温度,降低周围介质中CO2分压,并供给足够的热量。由于生料在分解炉内呈悬浮状态,基本上是单颗粒,传热面积大,物料温度在850℃左右时,只需几秒钟可使CaCO3的表观分解率达85-95%(一般入窑分解率)。
4、固相反应(放热反应):指生料中各成份之间相界面上的反应和物质迁移过程,主要生成C3A、C4AF、C2S等矿物。550~1280℃,当1100~1200℃时形成大量C3A、C4AF,C2S达到*大。化学过程。生料粉磨得越细、生料均匀混合、加入矿化剂等都能提高固相反应速度。
5、烧结反应:当达到*低共熔温度(硅酸盐水泥生料在通常的煅烧制度下约为1250℃),开始出现液相,1300~1450℃~1300℃,C2S+C→C3S。随着温度的升高和时间的延长,液相量增加,液相粘度降低,C3S不断形成,完成熟料的烧结过程。
烧结范围:指水泥生料加热至出现烧结所必需的*少液相量时的温度(开始烧结的温度)与开始出现结大块(超过正常液相量)时温度的差值。生料中的液相量随着温度升高而缓慢增加,其烧结范围就较宽,当窑内温度出现波动时,不易发生生烧或烧结成大块的现象;若生料中的液相量随着温度升高增加很快,其烧结范围就较窄。一般硅酸盐水泥熟料的烧结范围:150℃。
6、冷却:1300~1000℃,新型干法窑冷却带很短1-2m。主要放在冷却机进行,其目的:
6.1回收熟料带走的热量,预热入窑二次空气和入炉三次空气,提高窑、炉的热效率;
6.2迅速冷却熟料,以改善熟料质量与易磨性;
1250~1280℃:C3S → C2S+C:应快速越过该温度区间,C3S才能稳定存在;小于500℃时出现:β-C2S → α-C2S,体积膨胀10%,粉化现象,没有水硬性,影响熟料质量。
6.3降低熟料温度,便于熟料的运输、储存与粉磨。
二○○二年三月十四日
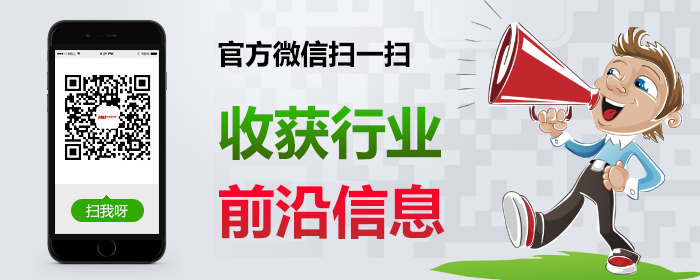